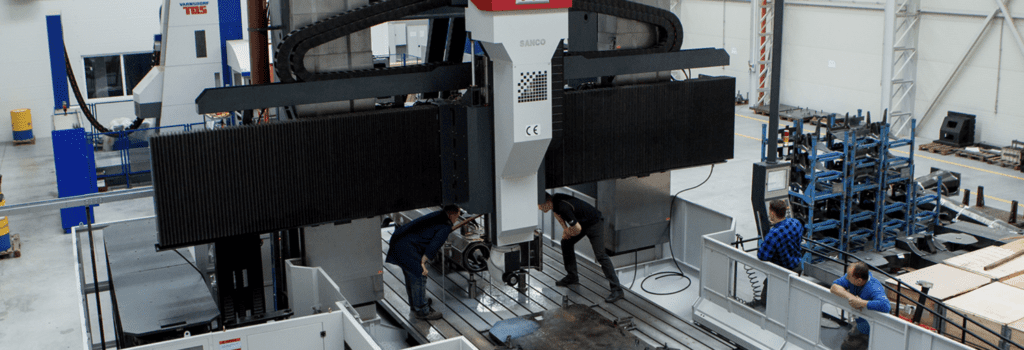
What is Theory of Constraints?
Theory of Constraints (TOC) is a business improvement methodology that has transformed manufacturing and other industries and sectors worldwide over the last 40 years.
It first emerged as a management philosophy based on Eli Goldratt’s influential business novel, The Goal, published in 1984.
In The Goal, Goldratt uses the example of a manufacturing plant facing closure to explain why traditional efficiency improvement methods fail.
The main character, Alex Rogo, embarks on a journey to uncover the key factor that’s destroying his plant’s performance.
Is his NCX10 machine the bottleneck? Or something more fundamental?
Along the way, Goldratt teaches a process of ongoing improvement for any flow system. He introduces the TOC approach to solve many common inventory and production management problems that bring manufacturing operations to the brink of ruin, including:
- poor manufacturing plant flow
- too much overtime
- slow throughput
- poor on-time performance, and
- flawed cost accounting
Since the publication of The Goal, Theory of Constraints has continued to grow, evolve and advance management best practices.
Today, the Theory of Constraints International Certification Organization (TOCICO) develops and administers certification standards and facilitates the exchange of latest developments in TOC. A global not-for-profit organization, TOCICO was established in 2001, with Montera CEO Jack Warchalowski and Executive VP Duncan Patrick as founding members.
TOCICO defines Theory of Constraints as:
A holistic management philosophy developed by Dr. Eliyahu M. Goldratt that is based on the principle that complex systems exhibit inherent simplicity, i.e., even a very complex system made up of thousands of people and pieces of equipment can have in any given time only a very, very small number of variables – perhaps only one (known as a constraint) – that actually limits the ability to generate more of the system’s goal.
Everything we do at Montera is based on the tenets of TOC and Lean Thinking.
TOC is the basis for our Flow Management System methodology, powered by Roadrunner software, that we use to deliver big step improvements for manufacturers worldwide.
What problems does TOC solve?
In manufacturing, TOC solves two big problems:
- Making too much of what you don’t need and not enough of what you do need
- Focusing your improvement efforts in the wrong areas
Theory of Constraints applications
TOC techniques have many applications, including business services (accounting / tax filings, insurance claims processing), healthcare (patient flow), mining, software development, IT deployment and more.
In a manufacturing setting TOC is used to:
- Increase productive capacity
- Improve on-time delivery
- Reduce inventory
- Reduce costs, and
- Increase net profit
What is a constraint in TOC?
As the name indicates, TOC philosophy revolves around the idea of constraints as limiting factors in achieving goals.
TOCICO’s TOC dictionary defines a constraint as:
The factor that ultimately limits the performance of a system or organization. The factor that, if the organization were able to increase it, more fully exploit it, or more effectively subordinate to it, would result in achieving more of the goal.
Where are the constraints in your operation?
To find the constraint(s) in your operation, you need to step back, like Alex does in the book, and look at the entire business.
Think of it like peeling an onion.
First, consider if the fundamental constraint is internal (within your operation) or external (in the marketplace).
Internal (operational) constraints
If you have too much demand and can’t meet your commitments, the constraint is internal.
In this case, TOC’s 5 focusing steps are a systematic way of managing the constraint. These steps will help you improve efficiency, throughput and overall performance. Here’s the process:
- Identify the constraint: Start by drawing a flow stream map and consider: where is the weak link in the chain? Which machine has the least capacity most of the time? Which machine or process creates the most problems for you?
- Exploit (optimize) the constraint: Fix or reorganize things to produce as much as you can through the constraint, so it works at full capacity.
- Subordinate all other activities to the constraint.
- Elevate the constraint: Invest in capacity related to the constraint (equipment, people, other resources) to produce more.
- Stabilize the system: Increase output via the constraint in relation to everything else in the plant, growing production of the entire plant.
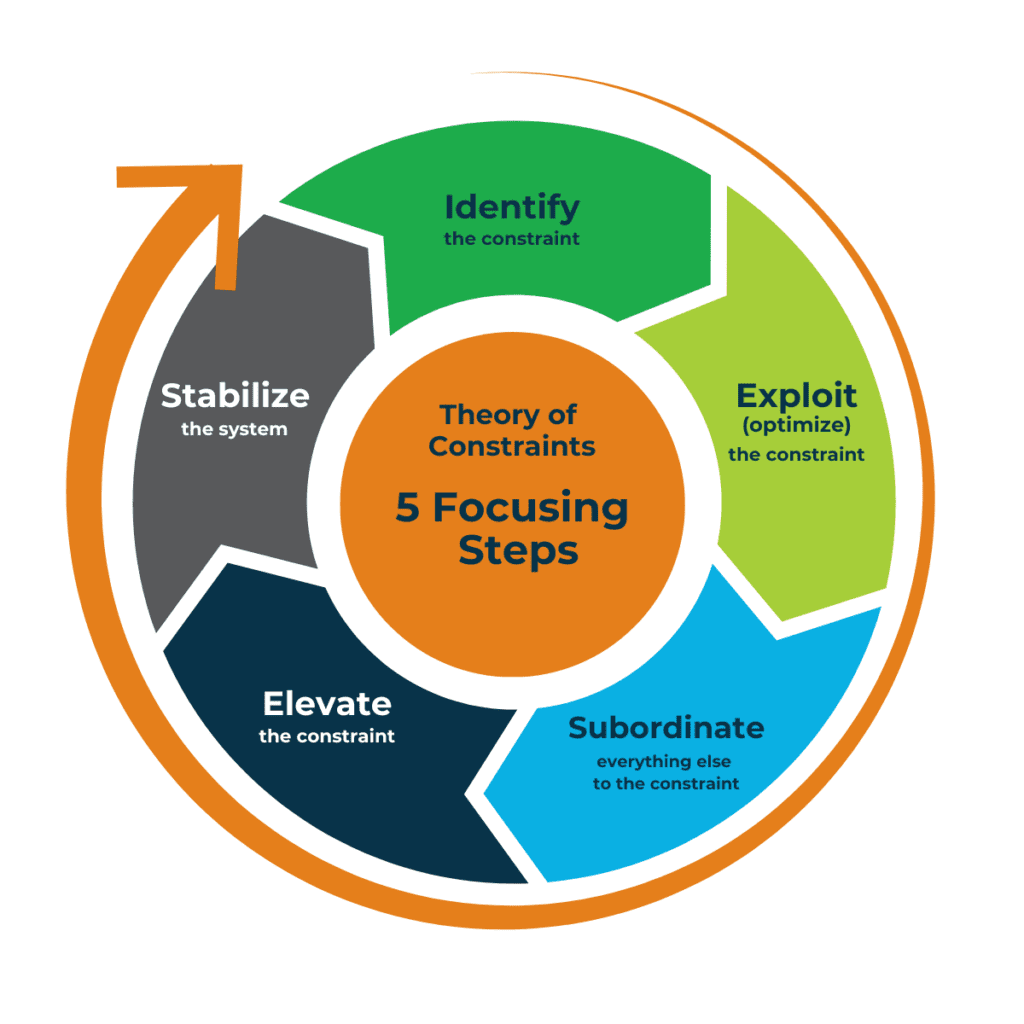
Note that, contrary to common wisdom, our objective is not to eliminate the constraint.
What we want to do is to create a continuous improvement process around the constraint that unlocks growth using TOC solutions like Demand-Driven Replenishment, Demand-Buffer-Rope scheduling and Critical Chain Project Management.
Focusing improvement efforts in the right areas
Another TOC solution, a continuous improvement process driven by Flow Issue Reporting, also helps manufacturers focus their improvement efforts on the right areas.
Flow Issue Reporting
Using Flow Issue Reporting (FIR) for all Work Orders to drive continuous improvement is a simple yet powerful approach.
FIR is not a replacement for Lean or Six Sigma as it does not show manufacturers how to improve nor provide a set of improvement tools.
It simply tells manufacturers WHERE to improve – to ensure the fastest achievement of significant bottom line results.
FIR tracks the biggest issues impacting the flow of orders through the entire manufacturing flow vs tracking issues that affect individual or departmental flow.
Work centre downtime reporting is only a small part of the Work Order Flow Issue Reporting process.
The biggest issues impacting flow ARE the biggest issues preventing manufacturers from achieving significant bottom line improvement.
Quite simply, shop floor supervisors or operators record the reasons why a work order is not where it is supposed to be; these reasons are then collected and put into a Pareto Diagram; management reviews these Pareto Diagrams weekly and prioritizes continuous improvement efforts.
Increasing bottom line impacts
Our experience suggests that when manufacturers use Flow Issue Reporting to drive continuous improvement, the number of projects leading to bottom line impact increases from two in 10 to nine in 10.
External (marketing) constraints
If demand is NOT sufficient to grow your system, then the constraint is external: it’s a marketing problem.
In this case we recommend using a Throughput Economics approach to assess market demand, pricing and profitability (more on this to come in a future article).
Once you better understand your market using Throughput Economics, chances are you’ll flood your plant with orders. Then we focus on exploiting your capacity.
To sum up, the good news is that many manufacturing challenges can be much better managed with Theory of Constraints approaches.
Manufacturing challenges? Let’s chat!