You’ve read The Goal
Now put that theory into practice via a hands-on and interactive role- playing workshop where you’ll discover the most-effective ways to put this breakthrough business book’s production lessons into action!
“The first course I have ever attended which kept everyone’s attention for the full duration! The combination of great content and great delivery.”
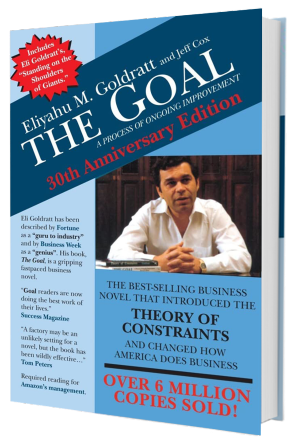
The Goal Simulation Workshop
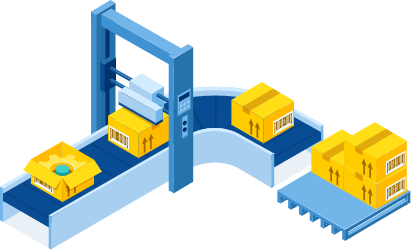
Plant Managers and C-Suite Executives are painfully aware that poor plant flow, overtime blowouts, poor on-time performance, and flawed cost accounting methods all destroy bottom-line results.
And many have – for years – known that the solution to their inventory and production management problems can be found in The Goal.
But applying the production and inventory improvement lessons of The Goal can be hard at first. Where do you start? How can you make mistakes and learn those valuable lessons without putting your plant (and profitability) at risk?
If you are keen to start implementing the ideas presented in The Goal at warp speed — and without falling for common traps — this hands-on workshop is for you. It will teach your management team via a realistic simulation how to use the techniques outlined in The Goal to:
- Increase productive capacity
- Improve on-time delivery
- Reduce inventory
- Reduce costs
- Increase net profit
Three rounds:
Process of on-going improvement
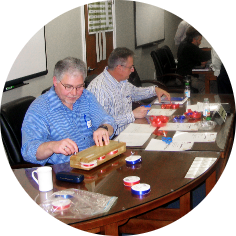
It all starts with a blank piece of paper and a rolling pin!
The Goal Workshop is an interactive 6-hour workshop where delegates run an imaginary plant and learn how to fast-track the principles of The Goal to turn a problem-riddled, money-losing venture into a highly profitable, perfectly synchronized manufacturing plant that delights its customers and makes serious money!
Over the course of the day you and your fellow participants will run an imaginary plant just like the one shown below. Your goal is to meet customer orders while reducing waste and improving revenue.
With your fellow team members, you will make 12 paper tubes of various lengths and sizes to represent your four main product lines as shown below.
Book a workshop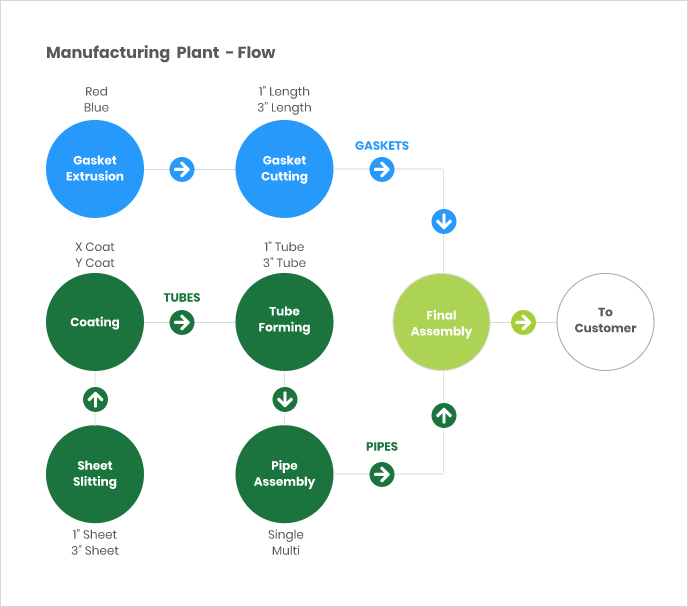
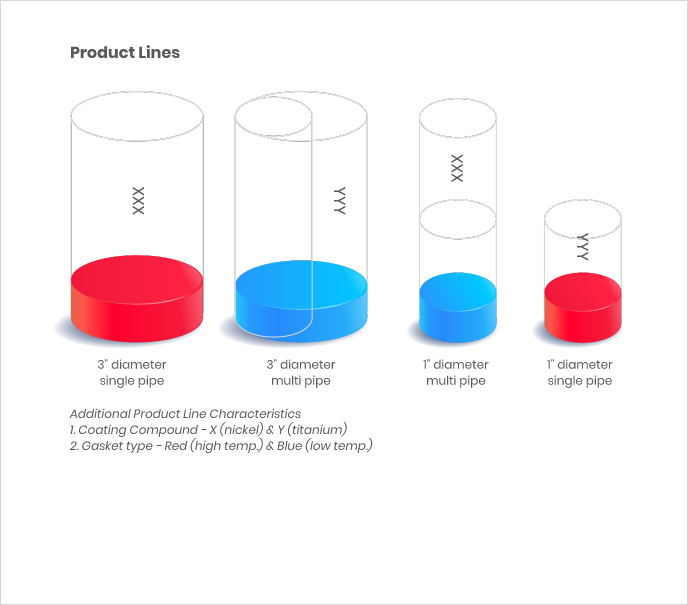
Your team will be challenged to meet customer order demand and maximize profit over three interactive rounds. In each round you will learn new techniques you can apply to increase plant productivity. Your challenge will be to improve plant efficiency within the following limitations:
- NO spending money
- NO alteration to product workflow or its design
- NO changes to job descriptions
- NO hiring / or firing
You will quickly realize that:
- Balancing production line capacity reduces its output
- Improving output / efficiency at each production step lowers line productivity
- Measuring productivity everywhere sub-optimizes performance of the plant
At the end of each round (there are three rounds in total), you will evaluate your plant’s operational and financial performance against your chosen approach to see how much money the plant has made (read lost) in the allocated timeframe.
One thing that will become quickly apparent is the unintended havoc traditional measures such as pieces per hour, uptime and full utilization at every work center can have on the performance of a manufacturing plant!
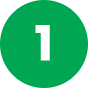
Round One
Traditional/Batch Manufacturing
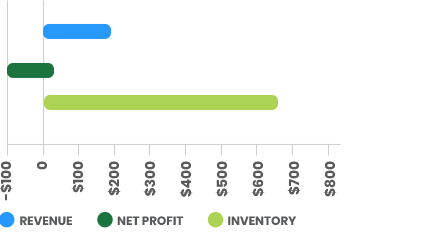
Round one tasks you to use the traditional batch manufacturing approach to meet demand forecasts and existing orders, based on two Manufacturing Principles:
- The best way to optimize a production line is to reduce waste everywhere and balance capacity.
- A resource standing idle is a major waste.
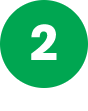
Round Two
LEAN Manufacturing
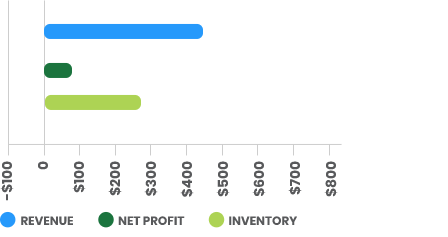
This round begins with an introduction to LEAN THINKING. You will be introduced to the most common LEAN manufacturing tools and techniques and their intended consequences.
Your team will then apply these techniques to the simulated plant to see what happens.
(Hint: most see a dramatic uplift in throughput and plant productivity utilizing a pull system and set up reduction.)
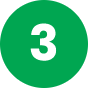
Round Three
Theory of Constraints
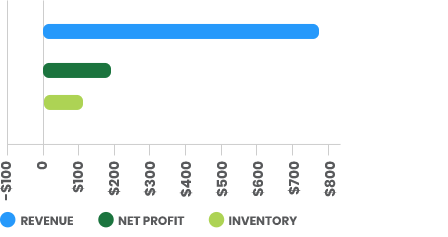
Here’s where the fun really ramps up. This round introduces the key ideas outlined in The Goal, namely the role of system constraint and buffer management in maximizing throughput.
You will learn, in contradiction to commonly held beliefs, the key to producing significantly more with the same resources is to:
- Unbalance the production line and maximize the output of one resource
- Choke the amount of Work-in-Process allowed in the plant
- Reduce the number of Continuous Improvement projects and focus on the resource that most often hinder flow
Key manufacturing concepts and topics covered
Theory of Constraints (TOC)
- Drum-Buffer-Rope (DBR)
- Constraints Buffer Management
- Protective Capacity
- Flow Issue Reporting
- Continuous Improvement process
LEAN Manufacturing
- Batch Size Reduction
- Kanban (push vs pull flow control)
- Line Balancing and Waste Elimination
- Set-up reduction techniques
- Waste reduction
Optional Day 2:
Supply Chain Management and Throughput Economics
There is an option to extend the workshop for a deep dive into advanced supply chain management concepts based on the principles of Demand Driven Replenishment (DDR) and Throughput Economics (TE).
You and your team will complete day two with an integrated business management framework built on the TOC methodologies for production (DBR), inventory management (DDR) and within a financial management (TE) model that you can apply to your own manufacturing plant for a dramatic improvement in business profitability.
Day two topics covered include:
- Product profitability using Profit Margin vs Throughput Velocity (TV)
- Relevance of standard costing
- How to effectively use sales forecast
- Demand Driven Replenishment (DDR) design principles
- How to right size your inventory levels – managing inventory imbalance
- How to maximize customer service level using DDR
You will learn:
- Why the best way to improve customer service is to lower overall inventory level
- Why evaluating customer pricing based on Product Margin lowers your profit
- Why you shouldn’t include direct labour in product cost
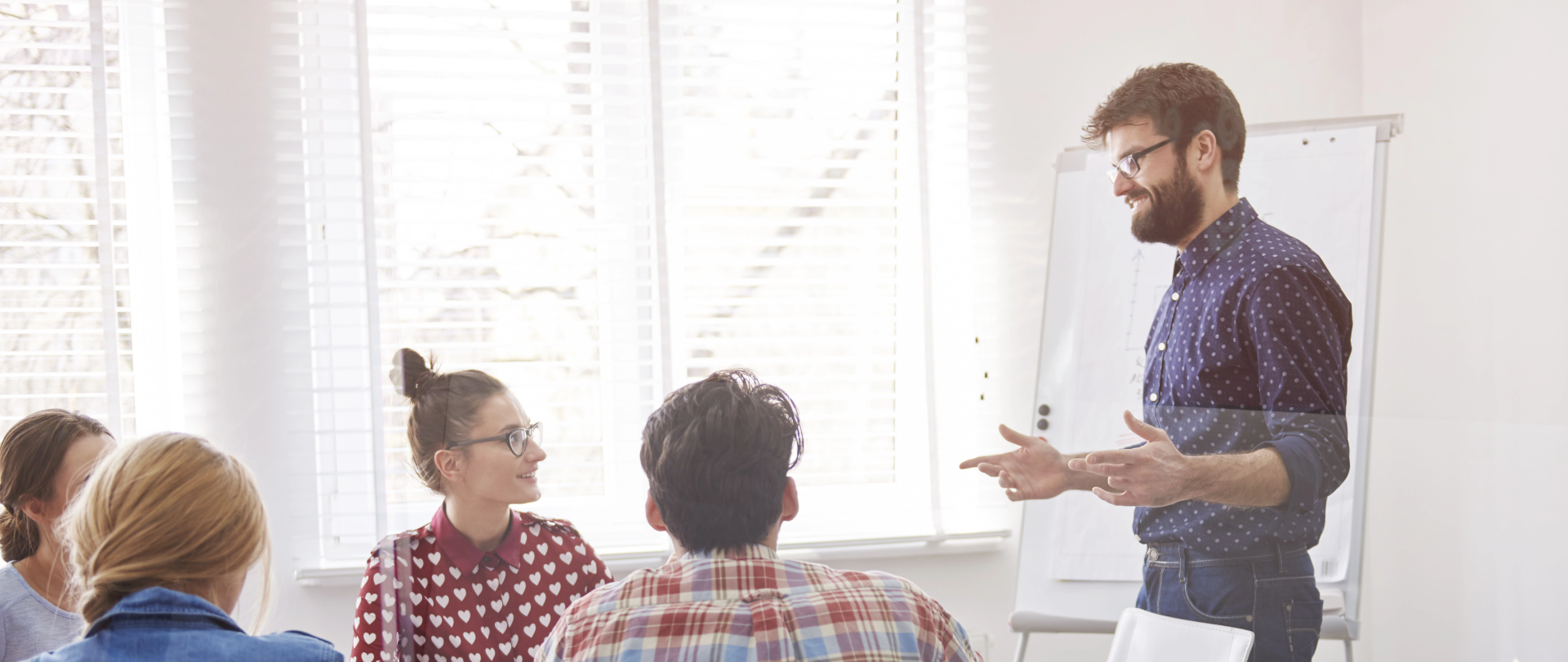
Attend this workshop
and you’ll learn these five things (plus much more)

How to improve manufacturing performance without spending money.

The effect of keeping machines, manpower and material busy through a transition from MRP to Lean to TOC.

LEAN manufacturing principles: batch size reduction, ‘Push’ vs ‘Pull’ flow control (Kanban), line balancing & waste elimination, set-up reduction and layout changes.

Drum-Buffer-Rope production management, Demand Driven Replenishment inventory management and Flow Issue Reporting based continuous improvement processes.

How to use Throughput Economics principles to maximize business profitability
Workshop formats
Option One: Inhouse
We will come to you and run The Goal workshop in your boardroom or nominated venue. The workshop is limited to 20 delegates in total.
Option Two: Group Workshop
Based on demand, we periodically run the workshop as an invitational event for multiple organizations at an upmarket city venue. The workshop is limited to 20 delegates in total.