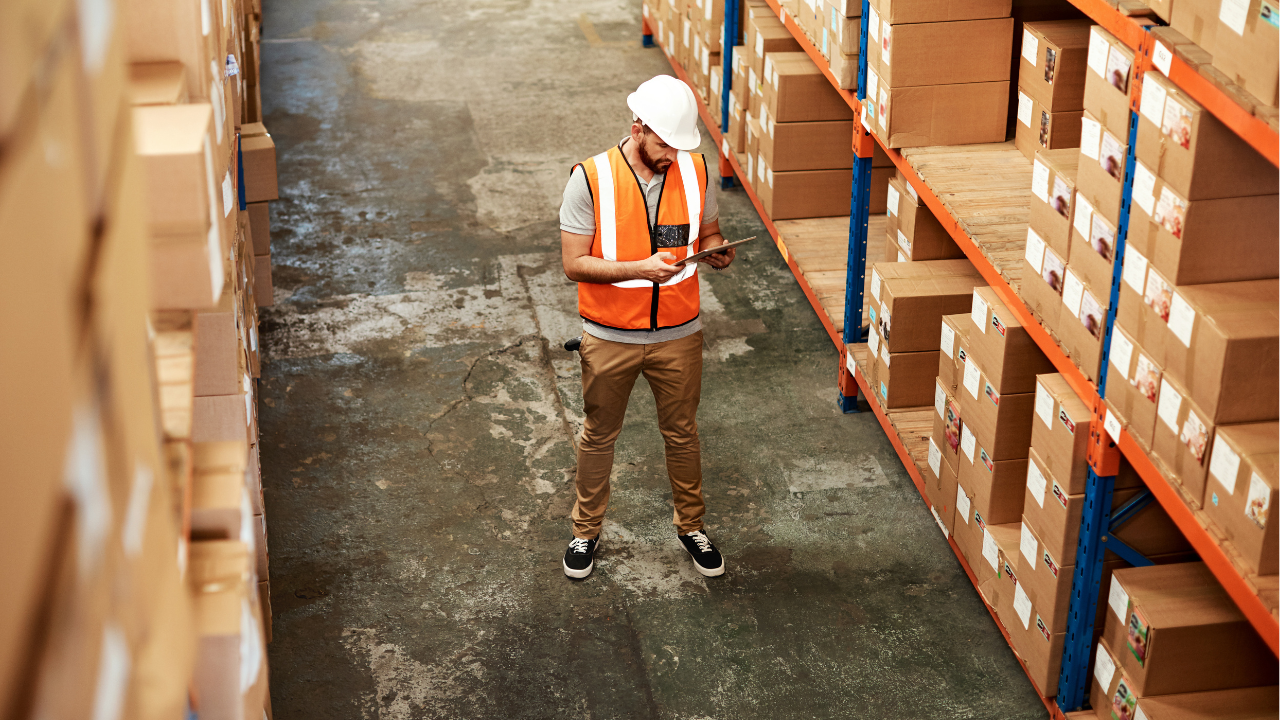
The case for demand-driven replenishment
All approaches to supply chain management aim to avoid a fundamental problem: stocking (and making) too much of some items and not enough of others.
This inventory imbalance predicament destroys plant performance:
- Cash flow dries up
- Throughput drops
- Sales slow down
- Expediting and overtime increase
- Your bottom line suffers
In our experience with customers worldwide, demand-driven replenishment (DDR) is the answer: it typically reduces inventory levels by at least 25%, driving costs down while increasing revenue.
This article explains the theory behind demand-driven replenishment, its advantages, and how to implement it in your manufacturing operation.
What is demand-driven replenishment?
Demand-driven replenishment – like demand driven material requirements planning (DDMRP) – is a Theory of Constraints (TOC) methodology for supply chain management that responds to customer demand in real-time.
It reduces the negative impact of supply chain variability by linking material availability (raw material, purchased parts, manufactured components and finished goods) directly to actual consumption.
DDR accounts for changing customer orders, as well as unreliable plant and supplier performance. It wholly removes the need for operator/management forecasting and guesswork based on historical data and trends.
The TOCICO Dictionary, published by the Theory of Constraints International Certification Organization, defines DDMRP [DDR] as follows:
A method of planning inventories that involves five components:
1. inventory positioning
2. grouping of parts into buffer profiles based on lead time; variability in demand and supply; whether the part is made, bought or distributed; and whether significant order multiples are involved
3. dynamic buffers
4. planning rules that tie supply orders to consumption
5. visible and collaborative execution
Push (MRP) versus pull (DDR) systems
Demand-driven replenishment replaces the forecast-driven approach of traditional material resources planning (MRP) with a dynamic pull-based system.
The TOCICO dictionary describes the difference between these approaches as follows:
“Traditional MRP systems are push systems based on forecasts of demand for finished products and generally focus on local optima throughout the supply chain. In contrast, DDMRP [DDR] is a pull system based on strategic placement of inventories across the supply chain with strategic buffers positioned for critical raw materials, work-in-process, finished goods and possibly distribution inventories. The system is based on measures such as buffer status that better reflect both a firm‘s and a supply chain‘s ability to respond effectively to customer demand.”
Benefits of demand-driven replenishment
Demand-driven replenishment has a significant positive impact on business profitability by reducing operational expenses and increasing sales at the same time.
The most significant positive effect of demand-driven replenishment is that it reduces total inventory: more than 90% of the manufacturers that Montera works with have seen inventory levels drop by 30% to 50%.
At the same time, it also dramatically reduces manufacturing lead time while significantly improving on-time delivery.
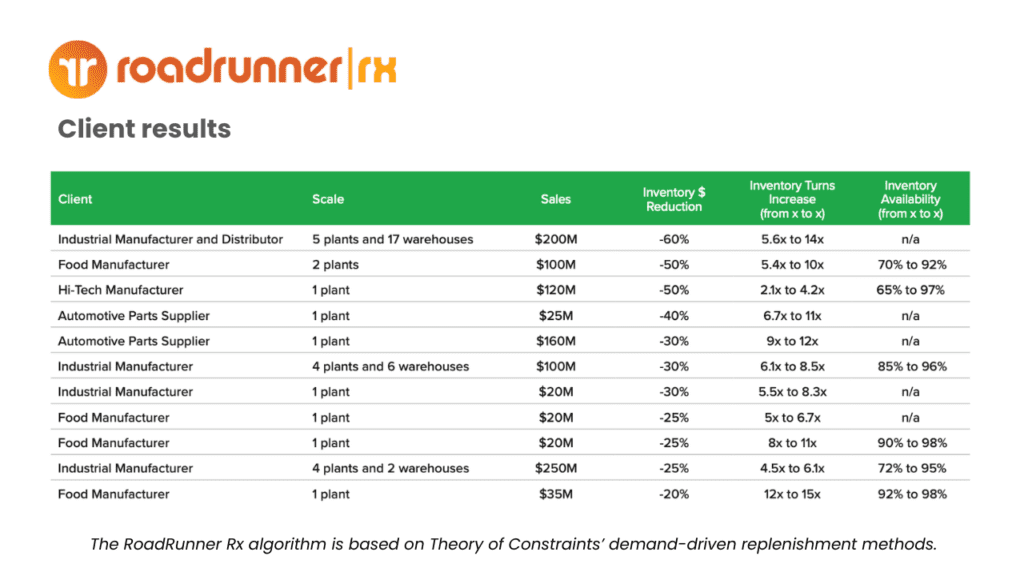
Demand-driven replenishment also dramatically reduces manufacturing lead time while significantly improving on-time delivery.
Other key benefits for manufacturers include:
- A more stable plant load
- Creates larger production batches for key resources
- Minimizes setup requirements
- Increases throughput
- Often reduces staffing requirements
- The ability to more often “make to stock” versus “make to order” (variable customer demand)
- Increases finished goods availability
- Improves customer service, and
- Increases sales
How to implement demand-driven replenishment
There are six key steps to implementing a demand-driven replenishment system:
- Define inventory requirements (using a DDR-sizing algorithm like Montera’s Roadrunner Rx) to set up buffer targets for key finished goods, raw materials, and sub-assembly items
Note: setting SKU-level inventory targets requires visibility to item transaction frequency, related lead times, consumption level fluctuations, and more.
- Establish a stock buffer “wall” with minimum required inventory level
- Replenish what’s consumed
- Absorb inaccuracy with buffer wall
- Adjust with feedback loop
- Once inventories are in place, a pull-based replenishment signal, in combination with other customer demand, creates the basis for generating the plant load.
Implementing DDR requires manufacturers to:
- ‘turn off’ their MRP system or Min / Max Inventory System for the purchase of raw material and purchased parts
- ‘turn off’ their forecast for the signal of “what to make” and “what to buy” and either make-to-order or make-to consumption (or both – depending on which strategy is appropriate), and
- de-couple their manufacturing flow by creating strategically placed purchased and / or manufactured component inventory buffers at:
- critical divergent or convergent points and / or
- at points in the manufacturing flow that are most susceptible to supplier or manufacturing variability.
Note that demand-driven replenishment doesn’t have to replace your ERP/MRP: it can work with your ERP/MRP to produce better results.
Strategic inventory buffers
The success of a demand-driven replenishment system rests on establishing strategically located inventory buffers that dynamically adjust (up or down) based on actual consumption.
These inventory buffers are a combination of:
- In-stock inventory (similar to kanbans)
- Inventory on the way (from your suppliers or in the plant)
They break supply chain dependence between:
- unreliable supplier deliveries
- variable customer demand
- and the plant
In this way, inventory buffers provide significant stability for the manufacturing operation.
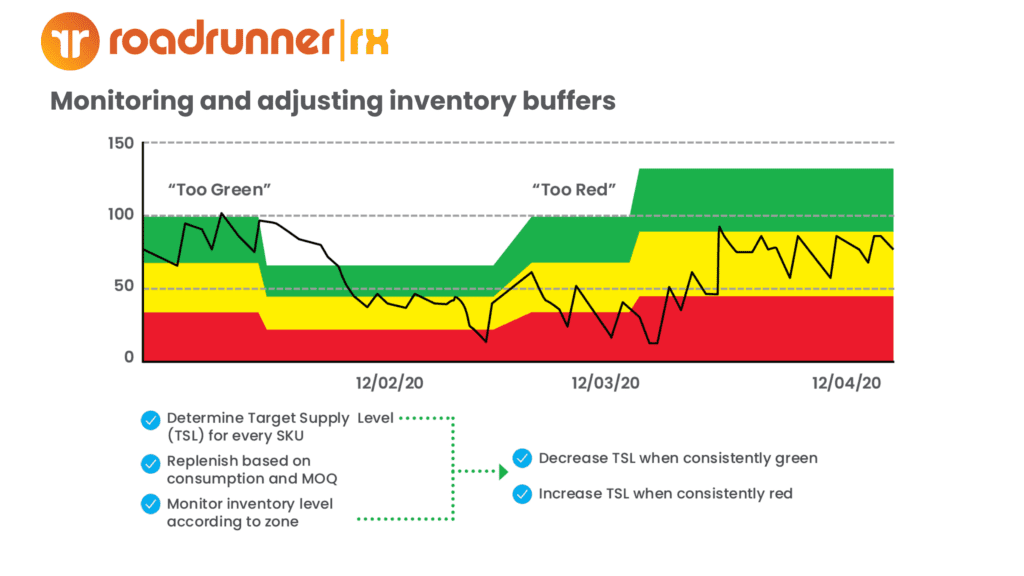
Learn more about dynamic inventory buffers in our article on MTO, MTS and Make to Availability production strategies.
Managing demand-driven replenishment complexity at scale
While relatively simple in concept, demand-driven replenishment can be challenging to implement when there are hundreds or thousands of SKUs involved.
We created Roadrunner Rx inventory management software to work with all ERP systems to address this complexity.
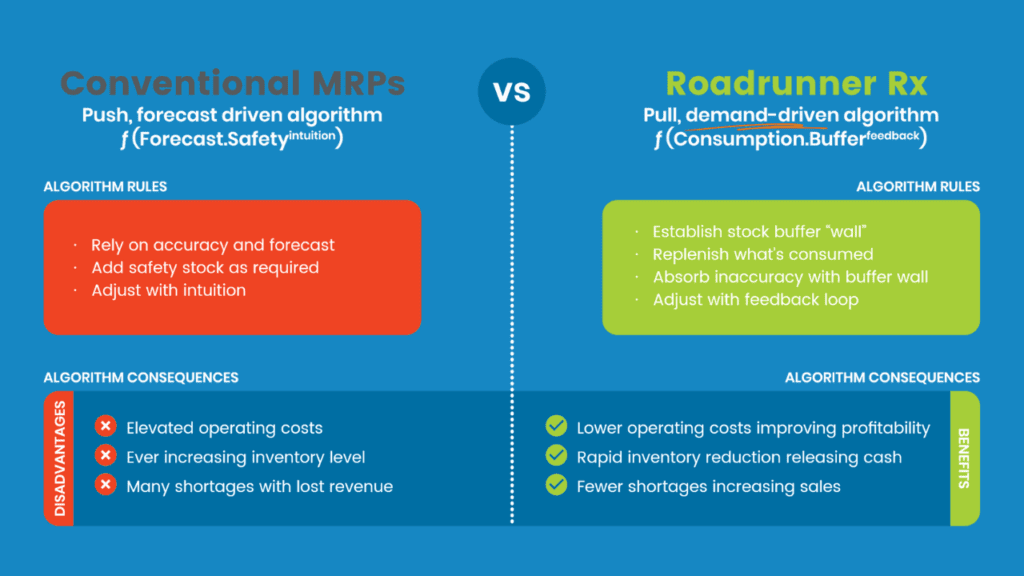
Roadrunner Rx uses an algorithm that draws on the well-established principles of demand-driven replenishment to deliver the following outcomes:
- Lower operating costs, improving profitability
- Rapid inventory reduction, releasing cash
- Fewer shortages, increasing sales
With our Roadrunner Rx Inventory Management Service, our experts manage it all for you.
Switching to a demand-driven replenishment approach is the ticket to getting the results you need: more business profitability by reducing operational expenses (less inventory, faster inventory turns) and increasing sales.
Get your FREE inventory imbalance report
Scores of manufacturers supplying complex multi-part subcomponents to global OEMs rely on Roadrunner Rx to balance inventory levels and improve supply chain efficiencies.
Learn more about our Roadrunner Rx Inventory Management Service and start with a FREE Roadrunner Rx inventory imbalance report: